Bad Weld vs Good Weld – How to Identify?
In different industries, welding is a very important application to combine different parts and equipment to obtain useful systems. They generally depend on the melting of the different materials to combine. They are non-destructive fastenings that we can not rip off the parts. But welding requires very good mastery and craftsmanship. And this depends on knowledge and experience. Here, we will explain all the aspects of the bad weld vs good weld. And you will understand all the required points about the welding methods.
How to Understand Bad Weld vs Good Weld?
First of all, understanding it requires a very different experience. Some people can understand the welding is good or bad with only one sight. But, there are important considerations to understand if a weld is good or bad.
Penetration of the Weld
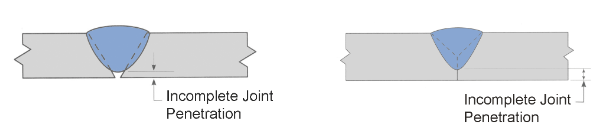
Penetration means, welding all the void between the different parts. The void can change according to the thickness of the material.
- Good weld: In a good weld, the penetration is deep enough to take all the space between the different workpieces. So the load distribution between these parts will be very uniform.
- Bad weld: As you can understand that the penetration is shallow for the bad welds. Because of this, they do not provide a uniform distribution of the load through the welding section.
Coloration
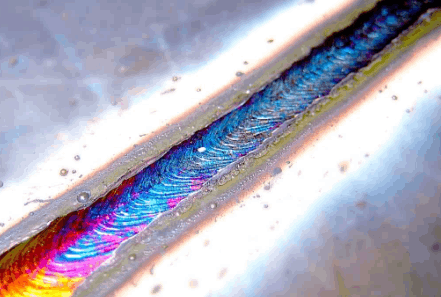
In social media, maybe you are seeing lots of “good” welds that get different colors ranging from purple to blue. This means, there is oxidation in the welding section caused by insufficient gas in the welding operation.
- Good weld: A good weld does not have any colorations on the welding sections. The color of the welded section must be uniform and colorless. This means the section gets enouıgh welding gas through the welding operation.
- Bad weld: In general bad welds can have colors as we stated above. These colors are very straightforward and the welded sectiın lacks oxygen.
Porosity
The uniformity of the welded section is very important. If there are discontinuous sections like the porosity, there will be very bad dissipation o the load through the welded section. And the welded zone will be much weaker if we compare it with the other sections of the workpieces.
- Good weld: In a good weld, there are no porosities inside the welded section. Porosities are the bubbles that have voids that make the welded section weaker.
- Bad weld: In the structures of the bad welds, we can encounter porosities.
Spatters
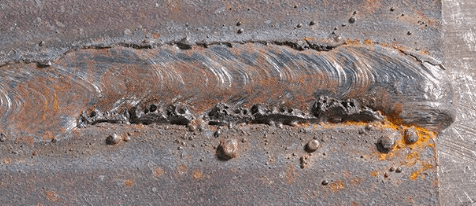
Spatters are another very bad thing that we are not expecting from the welded sections. You can see the spatters as little filler material splashes around the welded section. This is caused by poor material handling in welding operations.
- Good weld: In a good weld, there are no spatters around the welded zone. the experienced welder adjusts the amount of the material so that will not create a spatter around the welded section.
- Bad weld: If you see spatters around the welded section, you can conclude that this welded section is very bad.
Undercuts
Undercuts are the sections where the filler material does not fill the welded section properly. At the intersection points of the top surface of the material and the welded zone, you can see a hollow protrusion. Undercuts weaken the welded area.
- Good weld: In a good weld, you can not see any undercuts.
- Bad weld: In a bad weld, different kinds of undercuts will weaken the welded section.
Fusion of the Weld
Fusion means the connection between the filler material and the host material. Also fusion makes the welded zone stronger. You need to obtain a very good fusion between the different welded sections in general.
- Good weld: In a good weld, the fusion is very good between the host material and the filler material. An experienced welder can adjust the hat, amperage, and voltage to attain the best fusion between the welds.
- Bad weld: In a bad weld, the connection between the filler material and the host material is not good enough. This means the welded section will be much weaker than the normal applications.
Slag Formation
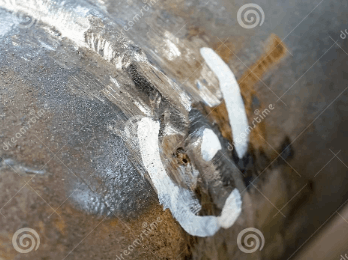
Also, slag is a very common problem that most welders are facing in general. Slags are the formation of little welding particles because of the oxidation of the filler material at high temperatures. We are using gas shieldings to prevent slag formation in the gas. So, if the control of the gas in welding operations is not good enough, slag formation can be a problematic issue.
- Good weld: In the good weld, the experienced welder will adjust the welding adjustments according to the type of welding to prevent slag formation.
- Bad weld: In the bad weld it is a very big probability that you can see there are lots of slag formations in the welded joint.
Welding Overlap
The overlap can take place because of the excessive use of the filler material on the welded zone. At the top of the weşded zone, you can see the formation of the excessive material that spreads on the welded material surface.
- Good weld: An experienced welder will adjust the level of welding material according to the void. So, the good weld to not have any overlaps.
- Bad weld: You can see the overlaps can form on the bad weld.
Crack Formation
The crack formation on the welded zone is a very important problem also. It can take place because of the uneven heat application on the welded zone. Cracks provide a weak joint between the welded parts. And because of these weak joints, the destruction of the structure can take place.
- Good weld: In a good weld, you can not see any kinds of cracks. All the welded section is crack-free.
- Bad weld: If you are seeing cracks formed, you can understand that this welded regişon is very poor.
These are the general considerations about the bad weld vs. good weld. So, it is very important to create a welded section that has a very uniform shape. A Uniform shape will provide much better aesthetics and much higher structural strength.
How to Test a Weld is Good or Bad?
Looking at the physical considerations on the welded zone to asses the welding is not the only dependable source of testing to asses if the welded zone is bad or good. Here, we will talk about the testing methods for welded zones.
We generally define the tests as destructive and non-destructive methods.
Destructive Testing Methods to Define Bad Weld vs Good Weld
Among the destructive testing methods, we generally apply force and load to test the welded joint. And the methods generally destructs the welding and we can not use this connection again. But if it destroys the stress levels that are intended to withstand, we can not use this welded joint also.
- Etch testing: This test is generally about the corrosion resistance of the welded joint. We use different acids to see the level of corrosion on the welded joints.
- Break tests: In break tests, we generally apply a very high level of loads to see if the system breaks or not.
- Tension tests: We apply tension on the welded joint and see if it complies with the level of specific stress.
- Hardness tests: Also standard hardness tests that we apply to different materials to see their hardness levels according to the Brinell, Rockwell, and other standards, we apply these to the welded joıimts.
- Bending tests: In these tests such as the Back Bend Test, we test the resistance of the bending moments of the welded jıoints.
- Fatigue tests: The general logic of the fatigue tests is, we generally apply a specific level of load on an alternating basis. After a cycle of load application, we check if the material is broken or not.
As you see above there is always a break or destruction danger for the welded joints.
Non-Destructive Test Methods
Also, these methods are about non-destructing the welded zone by testing if that welded zone is good or bad. These methods are also very common in most o welding applications. People looking for their welding applications to see if there are any problems with their welding applications.
- Visual inspection: This is the first and the most common testişngmethod for the welded areas. Professionals are looking at the welded zone and looking for if there are welding faults as we explained above.
- Dye penetrants: Penetrat tests are also visual inspections that are a much more advanced way of detection. In these applications, they are applied to the surfaces of the weld and inspect the penetrations on the welded zones. Penetrants make it much easier to see if there are any cracks and surface defects.
- Magnetic inspections: Also, we use magnetism to see if there are any faults or cracks in the welded area. The magnetic force will pull the weak sections.
- Eddy current inspection methods: Eddy electrical currents make it possible to visualize the internal cracks and unevenness of the welded zone.
- Ultrasonic inspections: Both transmission and reflection types of the ultrasonic inspection methods are applied to the welded area of the complex and important parts to see if there are any kinds of cracks inside them.
- Radiography: This is also very useful testing that clearly shows all the defects and internal problems inside the cracks of the welded zone. You need to check them clearly to see if there are any problems with them.
Bad Weld vs Good Weld Inspection for Different Welding Methods
We need to state that there are different welding methods that we need to consider. And there can be different points that we need to state about the bad weld vs good weld while considering them.
Stick Welding
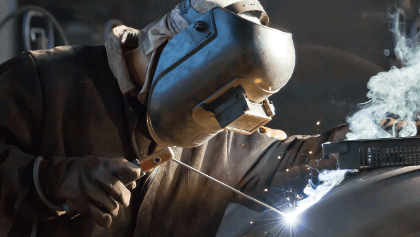
Stick welding or shielded arc metal welding is a type of welding application that we apply for the most basic duties. There is an electrode that is loaded with an arc. The filler material on the electrode is coated by shielding. So, creating and directing the arc to that place is very easy.
Good Stick Welding;
- If we visually take a look at the welded zone, we can not see any cracks or breaks. The structure is straight and uniform.
- Also, the thickness is the same for all the welding sections. The importance here, the welded zone has uniform mechanical characteristics that do not change with the changing length.
- Spatter is another problem that we need to consider in the stick welding application. If there are no spatters around the welded zone, we can understand that there are no kinds of problems.
Bad Stick Welding;
- If there are cracks and breaks are visible to the naked eye, the welding is very bad.
- Also if there is a spatter, the control of the filler material is not good for the welding operation. So, laying the material over the parts is not good enough.
- The thickness of the welding bead is not consistent. This means the load distribution over the welded zone is not uniform.
Oxy-Acetylene Welding

In oxy-acetylene welding applications, we use oxy-acetylene gas for the flame and the filler material. The operator must control two rods while applying the welding application. So, it requires good handling and experience from the operator.
In these welding applications, we generally weld soft and lowe melting point materials such as aluminum, brazing, and copper materials.
Good Oxy-Acetylene Welding;
- The welding bead is uniform and the load distribution through the welded section is uniform.
- There are no discontinuities such as globules or holes that can cause by the melting and boiling o the molten material.
Bad Oxy-Acetylene Welding;
- Unlike good welding, if there are holes and there is no uniformity along the welded section, it is not a good welding performance.
- The penetration of the workpieces is not good enough.
- Around the weld, we can see large globules.
TIG Welding
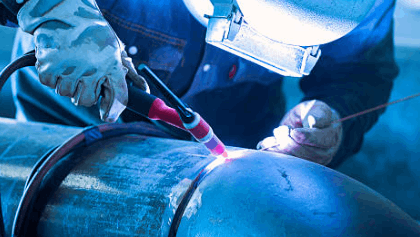
TIG or Tungsten Inert Gas welding is one of the most common welding applications that is used in industrial welding applications. They are generally very hard to apply welding applications for welding systems. Operator skill is very important. And Tungsten gas is used for the shielding of the molten material from outside applications.
Good TIG Welding;
- The uniformity for the TIG welding applications must be very good. You can see very good layered beads in these welding applications. the layering of these beads is very important and dependent on the welding operator. For example, in the Instagram and TikTok posts, you are probably seeing different layered and satisfying welded sections from the industrial applications. These welding videos and posts are generally TIG welding applications.
- In a good TIG welding application, you can see the layered, appealing pattern.
- There are no slags or burnouts on the welded system.
Bad TIG Welding;
- If you can not see any appealing pattern, probably this TIG welding application is not good.
- If there is no regulation along the welded section, the general application of the TIG welding is not good.
- You will see lots of burnout.
MIG Welding
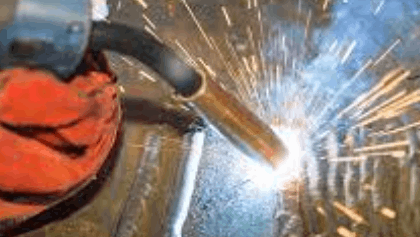
Also, Metal Inert Gas welding is one of the easiest ones to apply to metal applications. We generally use this welding application for industrial stainless steel, mild steel, and other applications.
Good MIG Welding;
- Good MIG welding is straight and uniform.
- You can not see any kind of slags and crackings on the surface of the welded zone.
- Also, there are no dips.
- Unlike TIG welding, there are no patterns in MIG welding. The welded section must be uniform and smooth.
Bad MIG Welding;
- If the strength of the welded section is not satisfying, the welding is not good.
- The beads are also very thin. You need to pay special attention.
- The uniformity is not good and you can see the different non-unişform patterns along the welded section.
How to Obtain a Good Welding?
Up to this point, you know the general important points about the bad weld vs good weld. And, if you know how to adjust the different parameters to obtain the best weld, you will be able to create the best-welded sections. There are different parameters that we need to consider about the welding applications.
- Use of electrode.
- Use of shielding.
- Wire feed speed and amperage.
- Travel speed.
- Voltage.
- Filler material.
Use of Electrode
For example for the TIG welding applicaitons, the manipulation of the electrode is very important to obtain the required patterns. Because the electrode is a very important part of welding applications. And the very high skill and experience required to obtain the required electrode motion in welding applications.
Shielding
Also, the adjustment of the shielding gas is very important. Shielding gas protects against the porosity and oxidation of the molten material at the welding zone. And if there is turbulence and airflow in the welding zone, the shielding will not be sufficient to save the welding. Also the welding will be very poor.
And also if you use the shieling gas in a very high way, you will provide contamination.
Wire Speed and Amperage
If the amperage is low and the travel speed is high, you will obtain insufficient filling action on the welding zone. And also spatters and burnouts are the general problems that are caused by the wire speed and amperage.
And if the wire speed and amperage are low, probably filler material overfilling and uneven sections will be the general problem that you will see.
So, a good and experienced welder must adjust the sufficient welding speed according to the situation and material to obtain a good weld.
Travel Speed
And travel speed of the electrode is a very important parameter to obtain a good welding application. You know that adjusting the width of the weld bead is very important. And if the travel speed is very high, probably you will have a problem with narrow beads. And if the travel speed is very high, you will probably have welded section that is very thick.
If you want to create a uniform bead with an optimum thickness, you need to apply the welding operation in a very good condition.
Voltage
The adjustment of the voltage is also very important for the welding application. With very low voltage, you will probably have no control over the welding thickness and height. And you will have spatters. And starting the welding operation will be problematic.
Also if you use very high voltage, you can not control the arc. The penetration will be inconsistent and you will have a problem with a poor and turbulent welding pool.
An experienced welder must adjust the voltage according to the user manual of the welding machine.
Filler Material
First of all, you need to select the good filler material that you need. And also the thickness of the filler material is very important. If you use a very thick filler, the voltage and electrical current will not sufficient to melt it.
And also very thin filler will cause the problem of very bad filling action and you will not be able to obtain the required uniform welding bead.
Last Words on Bad Weld vs Good Weld
As you see above, we explained nearly all the important details about the bad weld vs good weld. And we explained all the important points about the different welding types.
If you have additional comments and questions about this topic, please leave them below. Your precious feedbacks are very important to us.
Also, you can find other useful and insightful articles about welding on fmechanic.com!
Pipe Chain Clamps – What is It?
Welding Coveralls – Different Models
Welding Arm Pad Applications – Different Types and Styles
Carbon Fiber Welding Hood – Advantages and Review