Pin Welder – What is It? What are the Uses?
In installation of the insulation panels and other kinds of things like this, we use the pin welder systems. They are very useful systems that we can easily create a welded section for the panels. In HVAC and ductwork applications, the use of the pin welder systems are very common. Here you can find information about these systems that we use.
What is the Pin Welder?
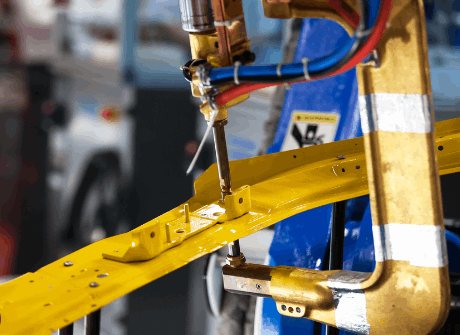
Pin welder is a special system that use stainless steel, aluminum, copper and other materials of studs that directly welds to the walls. So, they seem like brad nailers. The most general use of these machines is the insulation ductwork applications.
Most of these machines have capacility of nearly 30 welds per minute that provides very rapid installation of the insulation panels. It make the use of the welding and high strnegth applications very easy.
Also they generaly have thermal fan system that holds the motor and the recharging system of the pin welders cold. This increases the efficiency of the welding in a very good way. So, if you are thinking about the welding operations with studs, you can easily use them.
In general the stud sizes are M3 to M8 which means, 3mm to 8mm in daiemeter. So, they are very useful for different kinds of applications.
Most of the manufacturers are manufactruring welders in 110 VAC or 220 VAC according to the grid voltage of y our country. While you are selecting an application, please consider this thing.
Applications of Pin Welders
There are different kinds of applications of pin welders that we can consider. And you can use them in different kinds of systems like below.
- Automotive: The use of pin welders is very common in the automotive industry to combine the different car frames and other parts into chassis. Also, the combination of metal fasteners is very common in general.
- Aerospace: Also like the automotive, the combination of aerospace panels is very common with pin welder applications in general. They provide very compact and very good applications in general.
- Shipbuilding: In the shipbuilding industry, the use of pin welders is very common to combine the different kinds of interior trims, panels, decks, and other components.
- Heavy machinery: Also the fastening of the different parts such as the parts of presses, mills, and other industrial equipment, the use of the pin welders is generally very common.
- Electrical applications: To attach the electrical enclosures and control panels, we use pin welders in general.
- Construction: In the connection and attachment of the metal panels and studs, the use of pin welders is generally very common.
So, as you see above, there are different kinds of applications that we use for pin welder systems. Because of it, they are very common in the industry.
Advantages
Different kinds of advantages pin welder systems that we use the different kinds of applications that we explained above.
- Speed: The speed of the pin welder applications is very common in general. The automated applications make the pin welder applications very easy in different kinds of systems.
- Convenience: Also pin welders are very convenient systems in general. We can easily assemble the different kinds of applications on hard-to-reach surfaces in general.
- Strength: The strength of the pin welders are very common in general. So, if you are considerate about the strength, you can use these applications.
- Minimal damage: It is because of the very minimal point applications, they will not harm the secondary material in general. They will not harm the painted systems also.
- Safe: They do not create any sparks and this makes them they are very safe for different kinds of environments where flammable materials are present.
Disadvantages of Pin Welders to Consider
There are also different kinds of disadvantages that you need to consider if you want to apply pin welder systems in different applications.
- The required skill level is generally higher than the other conventional welding applications. This increases the total labor costs.
- The size of the welding application is generally limited. The diameter of the stud directly defines the total size of the pin welders in general.
- Limited joint configurations. You can only apply the pin welder systems to simple surfaces and contours in general. And this makes them less suitable for complex applications.
- Equipment costs: Also the costs of the equipment to make the pin welding is not cheap in general. You need to buy and maintain high-end products and applications to apply these systems.
Alternatives to Pin Welders that You Can Consider
These are the general alternatives that you can consider;
- Arc welding: Unlike pin welding, it is much more versatile welding that applies to many more different materials. But in general, it is a slower process than the other applications.
- Resistance welding: In automotive and aerospace applications, resistance welding is also very common applications. They use electrical resistance to create welded joints. Combine the different frames, they are generally very useful. They require much more detailed preparation in general.
- Gas welding: It is also a very different welding method that requires much higher preparation. But the application of various materials is much more common.
Conclusion on Pin Welder
These are the general points that we can state about the pin welder applications. If you have additional comments and questions about these systems, please leave them below. And also, you can find other useful articles about the welding operations in fmechanic.com!
Welding Bed – Prices, Advantages and Features
Welding Boots – Top Picks and Detailed Selection Guide
Pipe Beveler Machines – Guide for Pipe Welding