Protective Coatings and Sealants Guide
In many industries and applications, we are using protective coatings and sealants to make the structures and systems much more durable. There are different kinds of applications of them that give different kinds of superior features. Here, we talk about the general applications and their general features. And also you can learn the general industries.
Protective Coatings and Sealants
To improve the surface characteristics and features of the products and applications, we use protective coatings and sealants. Coatings are generally saved the surface from external conditions and sealants are for creating a system that waterproof or leakage-proof.
Purposes that We Use Them
There are different purposes why we use these applications commonly. And according to the purposes, the type of the application changes.
Surface Protection
As we stated above, the primary purpose of protective coatings is surface protection from external conditions. These external conditions and exposures are like this;
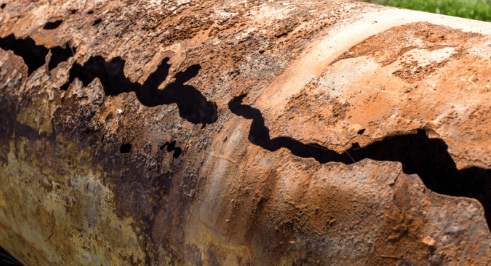
- Rust: Rust is a very common problem with eth iron-based parts such as steel and cast iron. The main reason for the rust is the oxidation of the iron. Because of the rust, the part loses mechanical strength and integrity. And also rust does not stop after a level like in the copper or aluminum applications. Because of this reason, there are different kinds of surface protection systems are created to prevent rust.
- Corrosion: Like rust, corrosion is also a very common problem that we face with critical mechanical components. When different types of materials such as steel, cast iron, brass, and bronze are exposed to air or salt water, they will lose material at a molecular level. So, this causes a problem that the loss of mechanical strength and integrity. For long-lasting systems, we use different protective coatings to prevent exposure to the outside environment to prevent corrosion. And the parts with corrosion resistance become much higher in terms of last.
- Abrasion: At dynamical parts that touch other surfaces, abrasion becomes a very important problem. The material lost its integrity and shape because of this frictional relationship. The most important example of it is the wheels of different systems. And surface treatment and coatings are very common to prevent this abrasion.
- Impacts: Also in dynamic systems, some surfaces of the machines or systems can be exposed to dynamic impacts. And if the material is not strong enough, unintended damages can take place. To increase the impact resistance of the systems, there are coatings and surface treatments are available.
- Moisture: Moisture is a very important parameter in corrosion and rust. So, protection of the surfaces and material from moisture is very important with several protective applications.
- UV light: On polymer surfaces, UV light has a degrading effect. And surface characteristics become less strong than the initial time. So, the use of surface sealants and coatings is very common to make the systems much more durable in UV light exposure.
- Temperature resistance: Temperature changes and high temperatures have also a very negative effect on the parts and materials. To decrease the total temperature exposure of the systems, we use temperature-resistant coatings on these applications.
- Scratches: This may be evaluated in the aesthetics but we are applying the coatings to prevent scratches on the surfaces of the products. Because scratches can cause starting points of the damage. And in terms of aesthetics, we do not want any scratches.
- Weathering: When a system or part is in contact with the open atmosphere, the wearing and abrasion will be severe. We call this phenomenon weathering. The common cause is UV light exposure, rain, snow, and temperature differences during the day. They are very important problems for such applications. We generally use different kinds of coatings to prevent weathering.
Obtaining Waterproof Applications
In general, to obtain waterproof applications, applying only protective coatings is not effective. Because we need to apply some internal sealants to the systems. For example, to prevent leakages in the piping applications, we need to use some sealants in the connections of pipes. They are not external solutions.
There are different kinds of applications that we need to provide waterproof systems to prevent water leakage and exposure.
Aesthetics
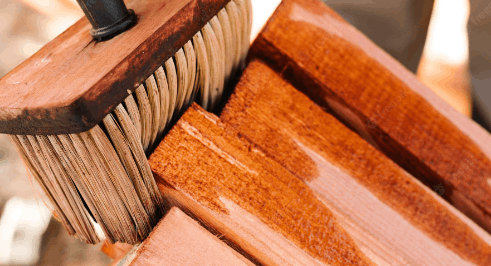
Aesthetics is a very important purpose that we are using the protective coating and sealant applications. Not only for protection, but the external looks of the products are also very important. And there are different coatings that we are using to obtain aesthetic applications.
For example, decorative coatings are a very common application in the packaging industry. We are coating the tin cans with different illustrations to make the much more attractive.
Also in the wood and plastic industries, the use of aesthetic coatings and paintings is very important. Floor varnishes and decking varnishes are very important examples of these coatings in general.
Types of Protective Coatings and Sealants
There are different types of protective coating and sealants to prevent the problems that we stated above. Let’s check them.
Epoxies
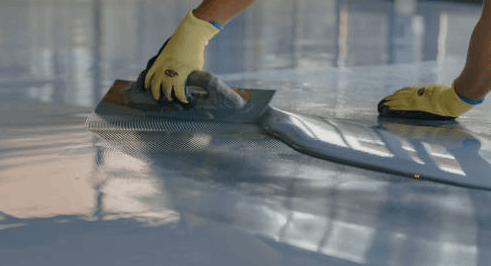
They are thermosetting polymers that cure with the application of UV rays. The starting form of the epoxies is liquid form. So, when we add an agent, the make curing process is very rapid. Curing means, the creation of extra chemical bondings inside the material. So, this curing process makes the liquid epoxy coating harden and creates a protective layer on the surface of the system.
The use of epoxies as a protective coating is very common in different applications.
- We generally use epoxies to prevent the weathering of different parts. They are very effective to prevent open atmosphere exposure.
- The epoxies are very good in abrasion resistance. The use of them is very common in the surfaces that touch with other surfaces of the systems.
One disadvantage of epoxies is, while they are curing, they release hazardous chemicals into the environment. This can be dangerous for the people who are applying this technique. So, there must be very high safety precautions whişle applying the epoxies.
Polyurethane Coatings
Like epoxies, the use of polyurethane coatings is very common. The application of this coating is nearly the same as the epoxies.
- Polyurethane has very good abrasion resistance. Because of this feature, the use of polyurethane material is very common in the wheels of different vehicles.
- Also, this coating is very good to reduce wear and tear.
- Another advantage of polyurethane coating is, they provide very good vibrancy and aesthetic feature to the systems.
- In terms of the costs, the application costs of polyurethane coatings are generally lower than the other applications.
There are also disadvantages to polyurethane coating applications.
- The weathering protection characteristics of this coating method are not good. Because of this, they are generally used for the systems that are available for indoor applications.
- Polyurethane material is flammable. Because of this reason, we can not use polyurethane material for inflammable applications.
- Like the epoxies, they are releasing very bad and poisonous gases into the environment.
Also, there is another polymer which is called Polyurea that has flame-retardant properties as well as other features that the polyurethane material has.
Zinc-Based Coating Applications
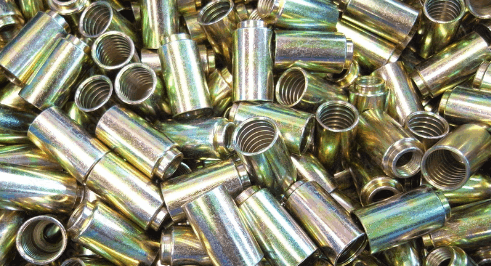
Also, the Zinc based coating applications are very common for metals. Unlişke polymer-based coatings are very common in industrial and machinery parts.
- The zinc coating provides very high-quality corrosion resistance to the system.
- Also, they provide a very good appearance to the surface of the parts.
The most important advantage of the zinc coating applications, we can not apply them to all kinds of materials.
Antifungal Coatings
Also, we apply polymeric resin applications to prevent biological contaminants in underwater applications such as fungus, mildew, bacteria, and spores. So, the protection of the system is very effective with these applications. For example, some HVAC and ducting applications are very common examples that we use these coating methods.
Coating Methods
We explained the general coating materials and their general properties. Here, we explain how to apply these coating materials. They are the most general methods that are applied in the industry.
Anodizing
For aluminum and copper-based applications, we are dipping the parts inside an electrolytic bath to create an oxide layer on them. We use the cathodic coating method to obtain this oxide layer.
In general, we do not want the oxidation of steel and cast iron materials. But the structure of the oxide layer for the anodized applications is very different for these systems. On aluminum and copper materials, oxidation takes place only up to a specific level. After that level, the oxide layer provides a protective layer to prevent the inner sides from oxidation and other external effects.
Powder Coating
Powder coating is also a very common application that we are using for different kinds of construction and aluminum parts. In the powder coating processes, we use an electrostatic force to bind the powders on the surface of the part. And we apply a curing agent to harden the powder on the surface. The powder material is generally synthetic resins such as epoxy.
Electroplating
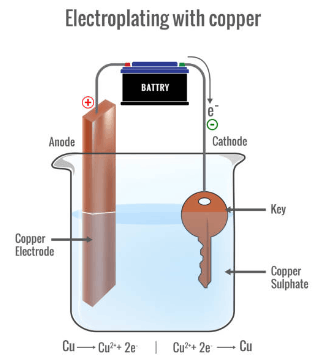
Electroplating is a very common technique that we generally apply to metal parts. The metal part is dipped inside the electrolytic solution. And the metal act as an anode. At the cathode side, the coating material which is generally zinc is transferred with the action of the electricity to the anode side. And this creates a protective layer on the metal part from the Zinc. there is a chemical bond between the coatişng and the surface of the material.
Painting
One of the simplest coating applications is that we can protect the different systems from weathering and other applications. They are very easy to apply and protect the systems from corrosion, scratches, and other damage. So, they are very useful for different kinds of applications.
Common Applications that We Use Protective Coatings and Sealants
There are countless applicaitons that we apply the protective coatings and sealants in general. e gave the most important ones here.
- Automotive: The use of galvanizing and Zinc coated metal parts is very common in automotive applications. And also the paintings on automotive applications are made with electrostatic painting applications.
- Aerospace: The surfaces of the aerospace applications such as planes are exposed to extreme atmospheric conditions. So, these surfaces must be very good enough to withstand these harsh environments. So, different high-quality paintings and coatings are used for the surfaces of these ssysteös.
- Construction: In the construction, we use different sealants to prevent water erosion and leaking water through the walls.
- Architecture: In general we use these systems to create very good and aesthetic applications.
- Furniture: On wooden pieces of furniture the use of varnishes is very common both for protection of the surface and aesthetic applications.
- Marine: The boat hulls and ships are exposing very several highly corrosive seawater. To protect the parts from this corrosive media, we use different protective coatings and paintings.
CASE: What is It?
If you are making research about protective coatings and sealants, you will probably coincide with this term. CASE means; Coatings, Adhesives, Sealants, and Epoxies. And people call this industry a CASE industry in general. So, do not stay a stranger if you hear this term in technical meetings and conversations.
Inside the Coatings of the CASE, we have both functional coatings to create a protective layer on the structures and applications and decorative coatings only for aesthetic applications.
In Adhesives, there are different materials to combine the different parts of the systems. They provide very good waterproof features to the systems.
Also, Sealants prevent water from coming into the system or leaking from the system.
And in general, we use Elastomers to obtain the adhesives, coatings, and sealants. EWasltomers are the class of polymers that have very extensive elastic properties in general.
Last Words on Protective Coatings and Sealants
So we are using protective coatings and sealants for different kinds of applications such as protection and aesthetics. And there are various types of them available in the market. To apply these different coatings and sealants, we apply different kinds of technical methods.
In the different areas of the industry, the use of protective coatings and sealants is very common in general.
If you have additional comments or questions about the protective coatings and sealants, please leave them below.